銅・真鍮などのレーザー加工なら共栄精機
ファイバーレーザー加工は、その高いエネルギー効率とビーム品質により、多様な材料のさまざまな加工において優れた性能を発揮します。真鍮や銅などの高反射性材料にも対応でき、精度と効率の両面で多くのメリットがある加工方法です。
共栄精機は、銅や真鍮といった高反射性材料にも対応できるファイバーレーザー加工機を有し、豊富な経験と高度な技術に裏打ちされた、品質重視の加工サービスを提供しています。レーザー加工での製品開発は、ぜひ共栄精機にご相談ください。
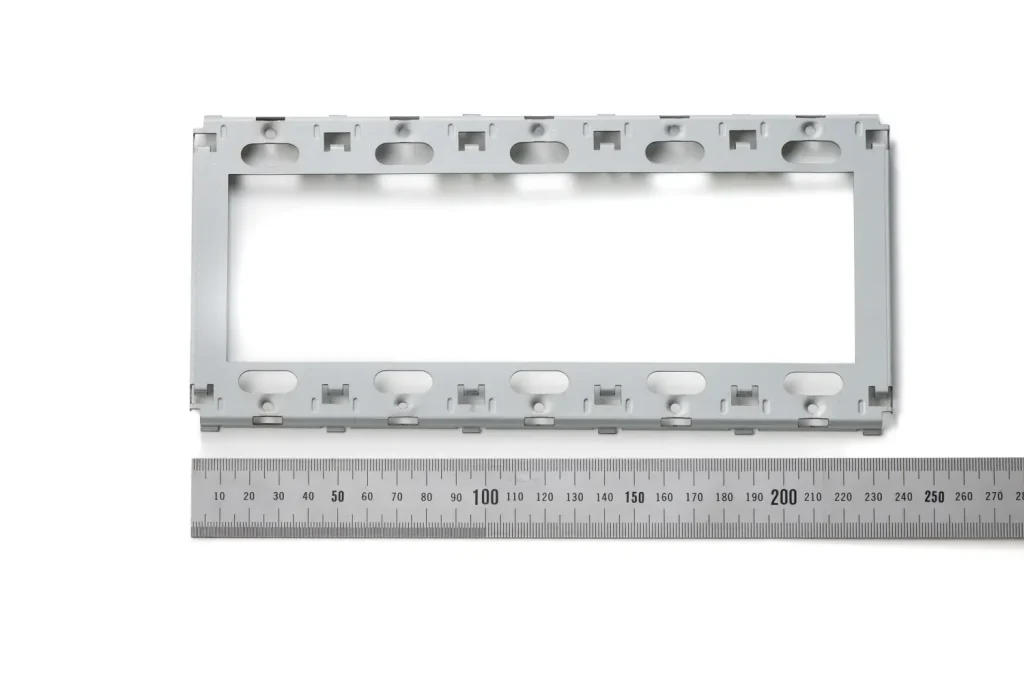
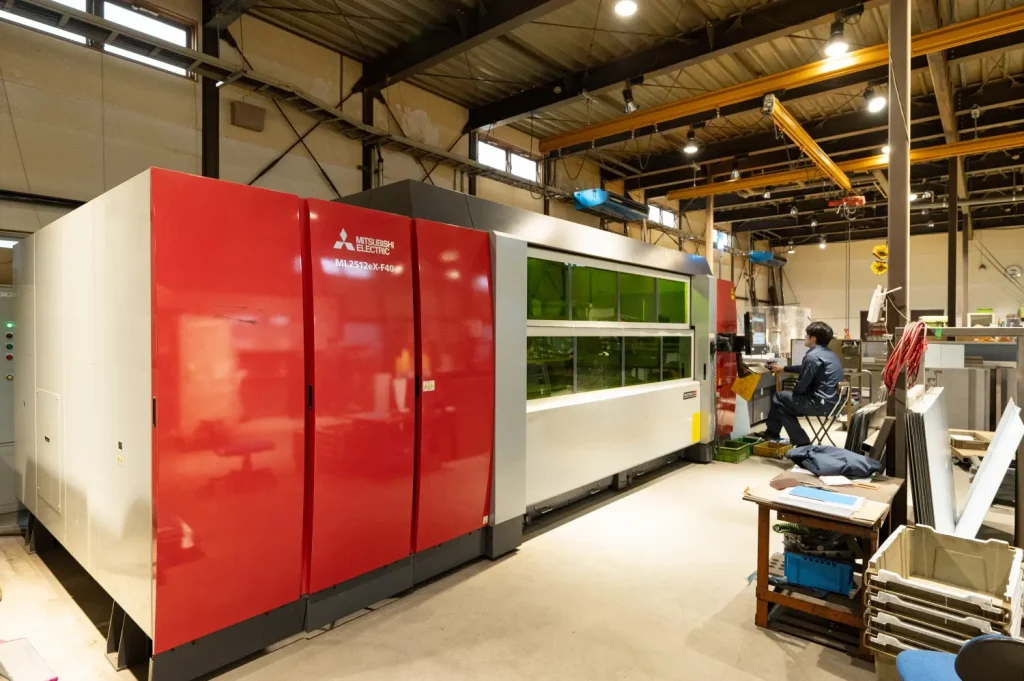
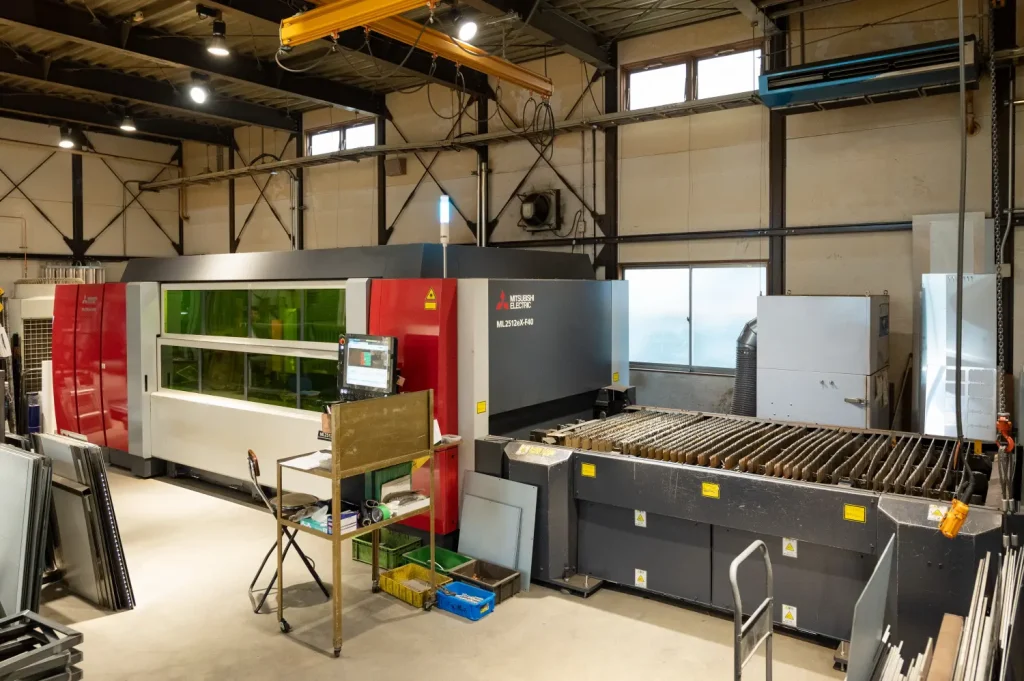
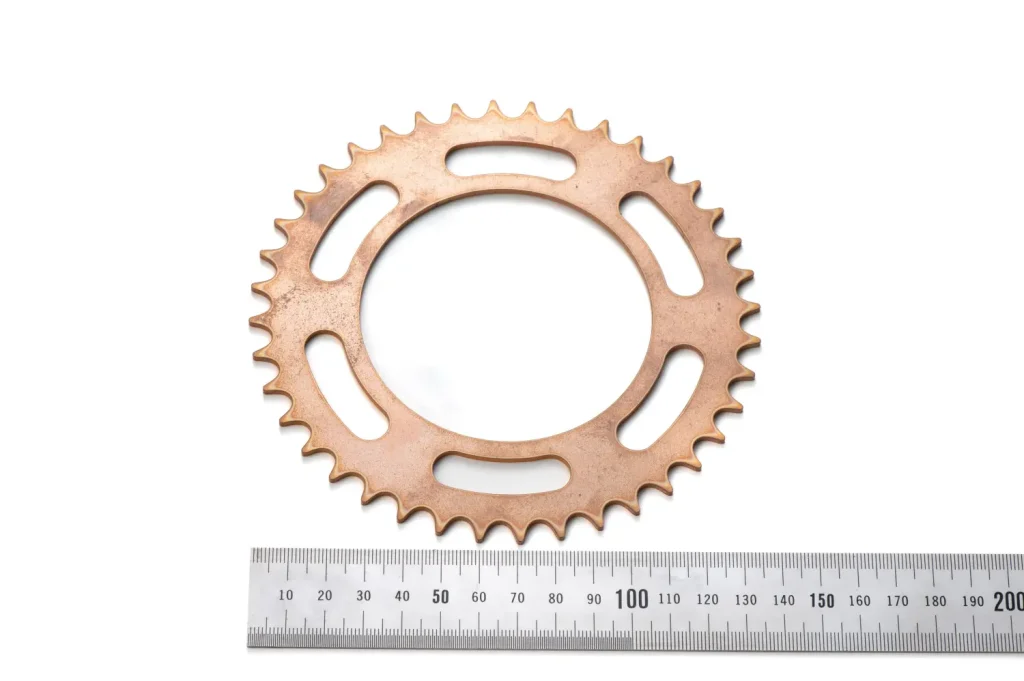
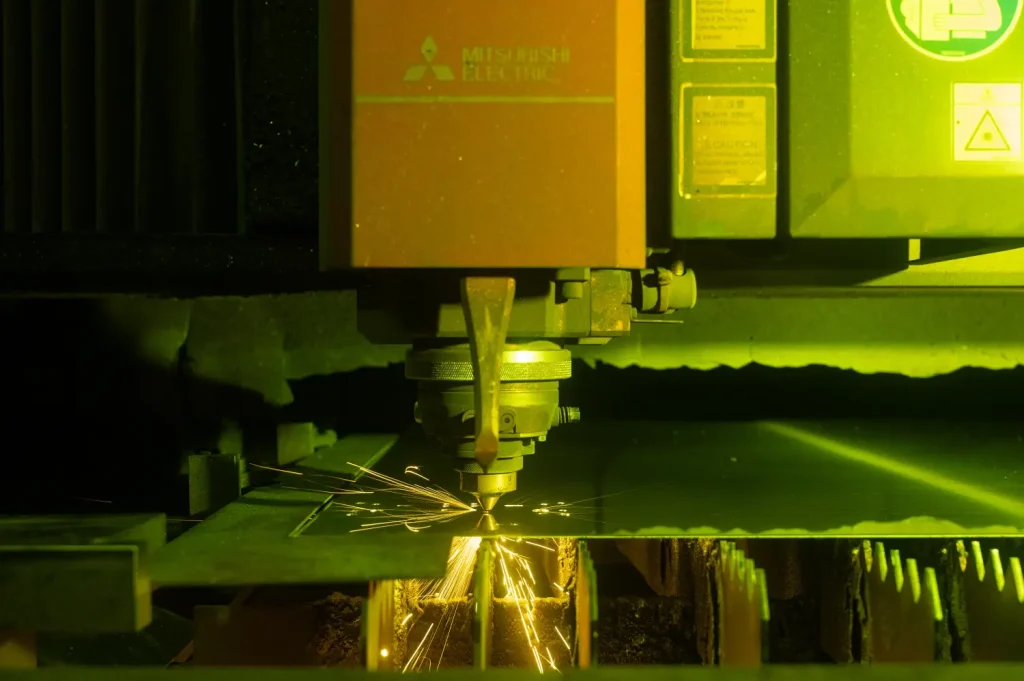
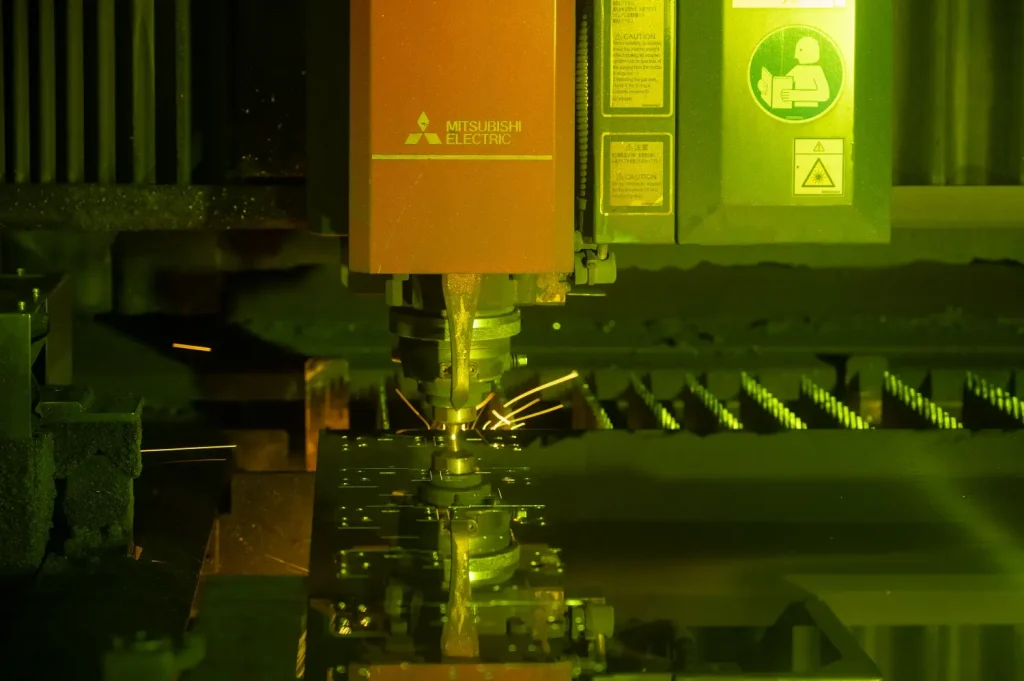
レーザー加工の基礎知識
ファイバーレーザー加工は、従来のCO2レーザーでは難しかった銅や真鍮に対しても、優れた加工性能を発揮します。高精度で効率的な加工を実現することで、コスト削減や生産性向上にも貢献します。ここでは、レーザー加工の基本からファイバーレーザーの特長、CO2レーザーとの比較優位性、真鍮や銅の加工時の注意点について詳しく解説します。
レーザー加工とは
レーザー加工は、金属や非金属の材料に対し、レーザー光を使って切断や穴あけ、マーキング、溶接などをおこなう加工方法です。ここでは、レーザー加工の特徴や用途など、基本的な知識を解説します。
レーザー加工の特徴
レーザー加工では、高いエネルギー密度を持つレーザー光を対象物に照射することで、局所的に高温状態を作り出して材料を融解・蒸発させ、精密かつ高速な加工を可能にします。従来の機械加工と違って非接触で切断や穴あけができることから、材料の変形や摩耗も少ないのが特徴です。
- 精密加工が得意
レーザー光は極めて細いビームを形成するため、微細な加工が可能です。取り込んだ図面データ通りに、非常に複雑な形状や小さな部品の加工も正確に行えます。刃物による接触がないため、バリもほとんど発生しません。 - 多様な材料に対応
レーザー加工は、金属やプラスチック、木材、ガラスなど、さまざまな材料に対して適用できます。ただし、銅や真鍮のような反射率の高い金属には不向きです。 - 作業効率が良い
レーザー加工機のセットアップと操作は簡単におこなえるので、すぐに作業を始められます。刃物の交換や研磨が不要である上に、コンピュータ制御による自動化によって生産性の向上も図れます。
レーザー加工の用途
レーザー加工は、多岐にわたる分野で活用されています。
分野 | 用途例 |
製造業 | 自動車部品、電子機器部品、航空宇宙部品、医療機器部品、金属筐体、架台 |
医療 | 医療用器具、インプラント、手術器具、歯科用機器 |
広告・展示 | 店舗看板(アクリル・木材・金属)、展示会のディスプレイ |
研究開発 | 新材料の特性評価、試作品、ナノテクノロジー、高精度な実験装置 |
建物・什器 | 建築金物、装飾金物、オーダーメイド什器 |
最も一般的な用途は、製造業での部品加工です。例えば、自動車部品や電子機器の製造において、金属やプラスチックの部品を高い精度で加工します。また、金属筐体や架台の製造においても、レーザー加工が重要な役割を果たしています。
医療分野では、各種医療用器具やインプラントの製作をする際に、レーザーを用いた加工技術が有用です。医療機器をレーザー加工で精密に作ることにより、患者の安全性や治療効果の向上に貢献しています。
さらに、広告・展示の分野でもレーザー加工の活用が有効です。アクリルや木材、金属プレートなどの素材に対して高精度で美しいデザインを施すことができるため、店舗看板や展示会のディスプレイの高品質化に役立ちます。
新材料の特性評価や試作品の製作においても、レーザー加工技術が用いられています。さまざまな研究開発の効率性を高め、新技術の迅速な実用化を図ることが可能です。
また、レーザー加工は精密板金の幅を広げています。建築金物や建築金具の製作のほか、店舗什器やオフィス什器のオーダーメイドなど、顧客の多様な要望にも柔軟に対応できます。
ファイバーレーザー加工とは?
ファイバーレーザー加工は、光ファイバーを用いて高出力で指向性の高いレーザー光を生成し、さまざまな材料を加工する技術です。切断や溶接に使用される連続発振の高出力レーザーと、微細加工やマーキングに用いられる低出力のパルス発振レーザーがあります。
従来のCO2レーザーやYAGレーザーに比べてエネルギー変換効率が高く、消費電力の削減と運用コストの低減も可能です。高いビーム品質により、銅や真鍮などの高反射材料にも対応できます。金属だけでなく、樹脂やガラス、木材など多様な材料を高精度で加工できるため、製造業や医療、広告、研究開発など幅広い分野で利用されています。
また、ファイバーレーザー加工機のレーザー光源の寿命は長く、頻繁なメンテナンスが不要です。これにより、生産ラインの稼働率向上と運用コストの削減にも期待できます。
CO2レーザーとの比較優位性
ファイバーレーザーは比較的新しい加工技術であり、CO2レーザーでは難しい加工にも対応できます。ここでは、CO2レーザーと比べてファイバーレーザーにはどのような優位性があるのか、仕組みや加工できる素材、コストと効率といった観点から説明します。
仕組みの違い
ファイバーレーザーとCO2レーザーでは、レーザー光の生成と伝達方法が大きく違います。
CO2レーザーは、二酸化炭素ガスをレーザー媒質とし、電気エネルギーを利用してレーザー光を生成する仕組みです。生成されたレーザー光は、ミラーを使って加工対象物に照射されます。
一方、ファイバーレーザーは光ファイバーを媒質として使用し、半導体レーザーから発振された光を増幅させる仕組みです。これにより、レーザー光の伝達効率が高くなり、ビーム品質も向上します。
ファイバーレーザーは、高いエネルギー密度を持つ細いビームを生成できるため、微細加工や高精度加工に適しており、加工スピードも速いです。対して、CO2レーザーは、比較的広いビームを生成し、広範囲の加工に向いていますが、ミラーやレンズの調整が必要で、定期的なメンテナンスが必要になります。
加工できる素材の違い
ファイバーレーザーとCO2レーザーでは、加工できる素材にも明確な違いがあります。
CO2レーザーは主に金属薄板の加工に適しており、木材やアクリル、プラスチック、ガラスなどの非金属材料に対しても優れた加工性能を発揮します。しかし、銅や真鍮といった高反射性の金属には不向きです。
ファイバーレーザーは高いエネルギー密度により、CO2レーザーでは加工が難しい材料でも、精密かつ効率的に加工できます。幅広い材料の加工に対応でき、銅や真鍮、アルミニウムなどの高反射性の金属の加工でも問題ありません。
コストと効率の違い
一般に、ファイバーレーザーのほうが導入コストは高くなりますが、ランニングコストではCO2レーザーに勝ります。
ファイバーレーザー加工機は、光ファイバーを使用するためエネルギーロスが少ないのが特徴です。機械自体は高価なものの、消費電力を効果的に抑えられるため、長期的なコストパフォーマンスは優秀です。
CO2レーザー加工機は比較的安いのですが、エネルギー効率がファイバーレーザーより低いため、ランニングコストが高くなりがちです。また、ミラーやレンズの定期的なメンテナンスも必要になるため、その分のコストやダウンタイムが発生します。
作業効率の面でも、全体的に見ればファイバーレーザーの方が優れています。高密度エネルギーのおかげで高速な加工が可能で、厚みのある金属材料の切断や複雑な形状の加工では、特に真価を発揮します。CO2レーザーは非金属材料や薄い金属板の加工は得意ですが、厚い金属の加工は時間がかかってしまうため非効率です。
真鍮・銅の加工における注意点
真鍮や銅のレーザー加工では、これらの金属が持つ高い反射率と熱伝導率が課題となります。これらの金属を加工する際にレーザー光の反射や熱の拡散が発生しやすく、結果的に加工精度を低下させる恐れがあります。
レンズの反射問題
真鍮や銅は高反射性金属であり、レーザー照射に対する反射光がレンズや光学系に悪影響を及ぼすことがあります。特に高出力レーザーの反射光がレンズに戻った場合には、熱によるダメージや焦点のズレを引き起こしてしまうでしょう。
真鍮や銅のレーザー加工におけるレンズの反射問題には、以下の対策が有効です。
・高反射性材料に対応したレーザー加工機を使用する
例えば、反射光を吸収するコーティングが施されたレンズを使用すれば、影響を最小限に抑えられます。また、レーザー光の照射角度を工夫して、反射光が直接レンズに戻らないように設定することも効果的です。
・冷却システムを導入する
レンズや光学系に適切な冷却装置を設置することで、熱によるダメージを防ぐことができます。加工環境の温度管理も徹底して、レンズの熱膨張や焦点ズレを可能な限り抑えることが重要です。
・定期的なメンテナンスを実施する
レンズや光学系の清掃を定期的におこなって、反射光によるダメージや汚れが蓄積しないようにします。さらに、レーザー出力や照射時間を材料に合わせて適切に設定し、過度な熱の発生を抑えます。
加工精度の問題
真鍮や銅のレーザー加工では、精度を維持するのが難しい場合があります。熱伝導率が高い金属は、レーザー照射で発生した熱が急速に拡散してしまい、加工面に影響を与えるためです。これには、以下のような対策を講じて対応します。
・レーザーの出力を調整する
高出力のレーザーを使用すると、熱の影響が大きくなりすぎて加工精度が低下するリスクがあります。適切なレーザー出力を設定し、必要十分な加工深度と速度を維持することが重要です。また、パルスレーザーなら瞬間的な高エネルギー照射が可能で、熱影響を軽減できます。
・アシストガスを使用する
レーザー加工の熱による金属材料の溶融や反応を防止するには「アシストガス(窒素やアルゴン、酸素など)」を使用します。適切な量のアシストガスを供給することにより、加工精度を維持すると同時に、火花の発生や蒸発ガスの引火も防ぎます。
・加工条件を最適化する
加工速度や焦点位置、ガス圧力などを適切に設定し、加工条件を最適化することが重要です。特に溶接では、スパッタガスが発生しやすいことにも注意しなければなりません。